The Bottom Line
UpNorth Group needed to monitor dark kitchens at national scale with an IoT system that could handle complex, industry-specific challenges. We delivered an enterprise-grade platform that processes 1000+ data points per hour with the reliability and compliance that commercial food service demands.
Data Points
Monitored per hour
Sensors
Per kitchen monitored
Uptime
Fault-tolerant design
Project Summary
Kioti is a fully integrated Supervisory Control & Data Acquisition (SCADA) solution for managing, monitoring and reporting on critical assets in commercial kitchens. By tracking a wide range of data points, from environmental conditions to resource consumption, Kioti provides operators with a streamlined, comprehensive tool that allows them to control their units with just a few taps on a mobile app or tablet screen.
The Problem
UpNorth Group, a leading enterprise covering diverse industry sectors from data centres to foodservice equipment, faced a significant challenge. They needed a large-scale comprehensive solution to monitor and control dark kitchens (restaurant kitchens selling meals on a delivery-only basis) on a national scale. The solution needed to be accessible through mobile apps and tablets stationed at each kitchen unit.
The challenge was complex: create an enterprise-grade IoT platform that could handle the unique requirements of commercial food service, maintain HACCP compliance, process massive amounts of real-time data, and present it all through an intuitive interface that kitchen staff could actually use.
The High-Stakes Challenge of Enterprise IoT
For UpNorth Group, this wasn't just about building monitoring software – it was about creating a system that could scale nationally while maintaining the reliability that food safety demands. Dark kitchens operate on tight margins with zero tolerance for downtime, especially when it comes to temperature monitoring and HACCP compliance. A system failure could mean food safety violations, lost revenue, and regulatory issues.
The Critical Challenges
The solution needed to integrate with dozens of different sensor types, handle complex data processing in real-time, and provide intuitive controls for kitchen staff who aren't necessarily technical experts. Most importantly, it needed to be absolutely reliable – in commercial food service, system failures aren't just inconvenient, they're potentially dangerous.
Our Solution: Enterprise-Grade IoT Innovation
We designed and developed a comprehensive SCADA solution that combines cutting-edge IoT technology with practical usability. Our approach focused on creating a system that could handle the complexity of commercial kitchen operations while presenting information in a clear, actionable format that empowers kitchen operators to make informed decisions quickly.
How We Solved It
Enterprise-Grade IoT Architecture
Designed a robust, fault-tolerant system capable of processing over 1000 data points per hour with real-time monitoring and automated alert systems.
Tesla-Style Interface Design
Created an intuitive, energy-efficient dark theme interface optimised for tablet use, making complex data accessible to kitchen staff of all technical levels.
Creative Problem-Solving Approach
Applied innovative solutions to complex and unexpected scenarios, adapting quickly to industry-specific challenges and regulatory requirements.
Design and Development Process
Before development began, we conducted comprehensive consultations with UpNorth Group to understand their requirements in full detail. We explored different technology stacks and their advantages, determining how each technology would scale with their needs. Kioti described their UI requirements as a 'Tesla Tablet Style Interface', which we designed to be intuitive, energy-efficient, and modern.
The dashboard provides a comprehensive overview of key kitchen metrics including equipment health status, HACCP temperatures, air quality, and system status, all presented through an sleek, dark-themed interface.
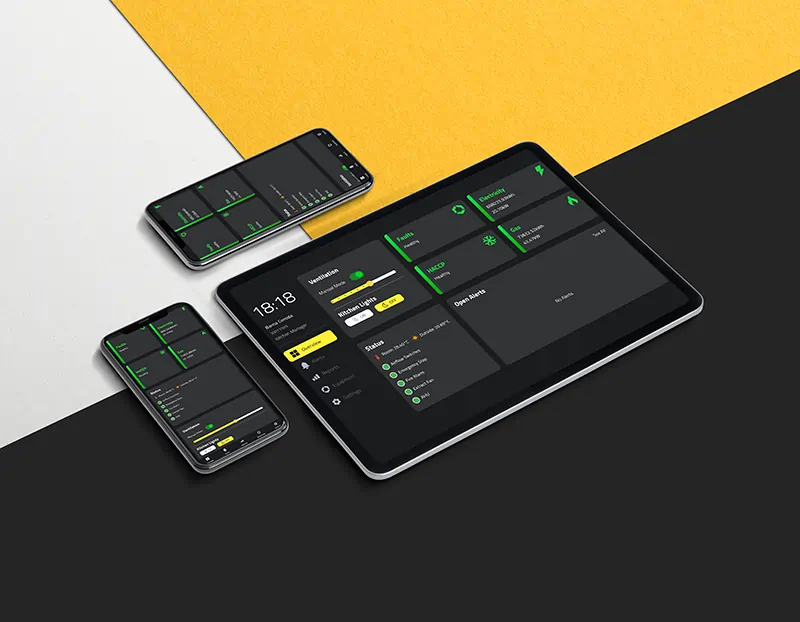
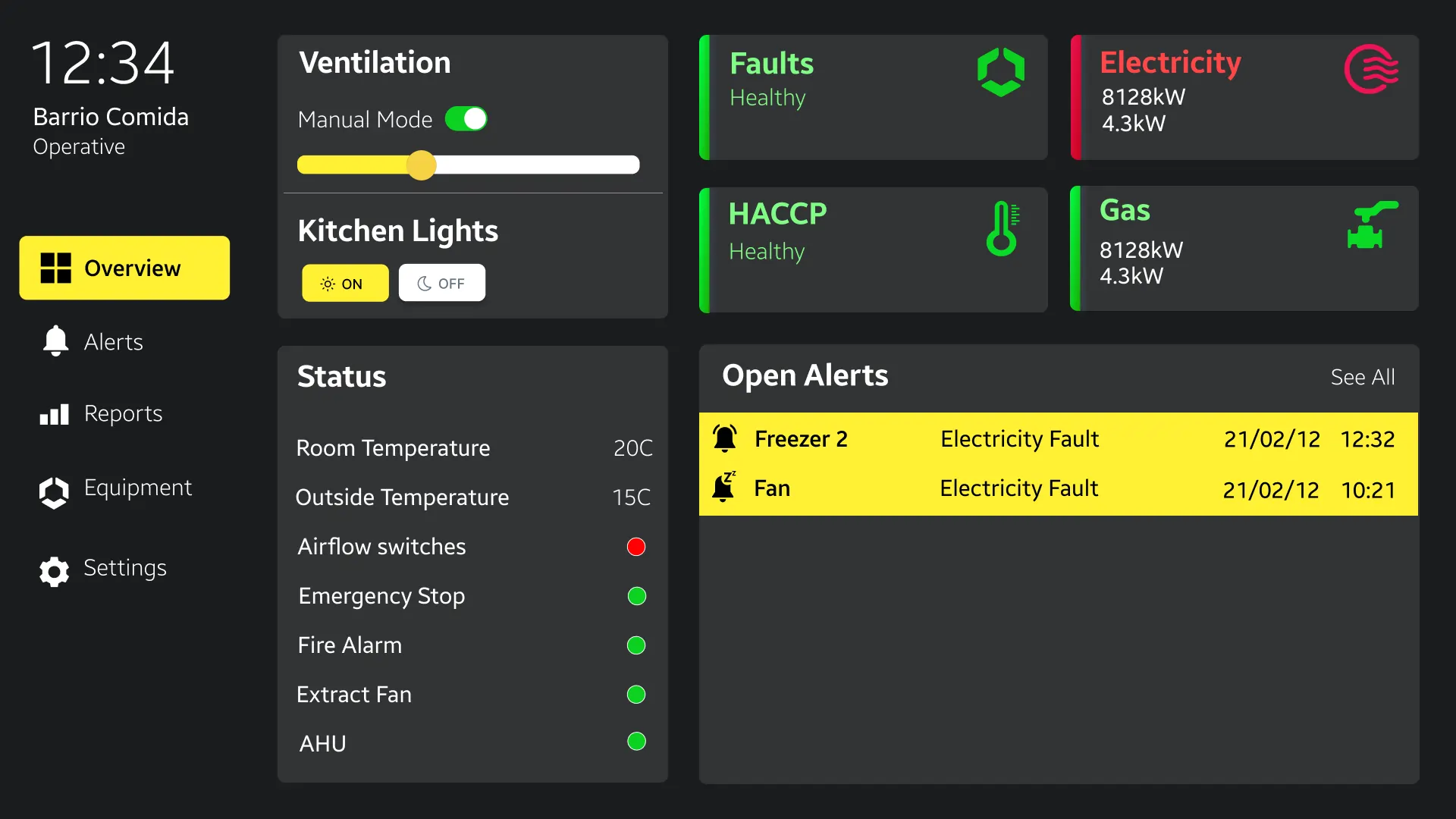
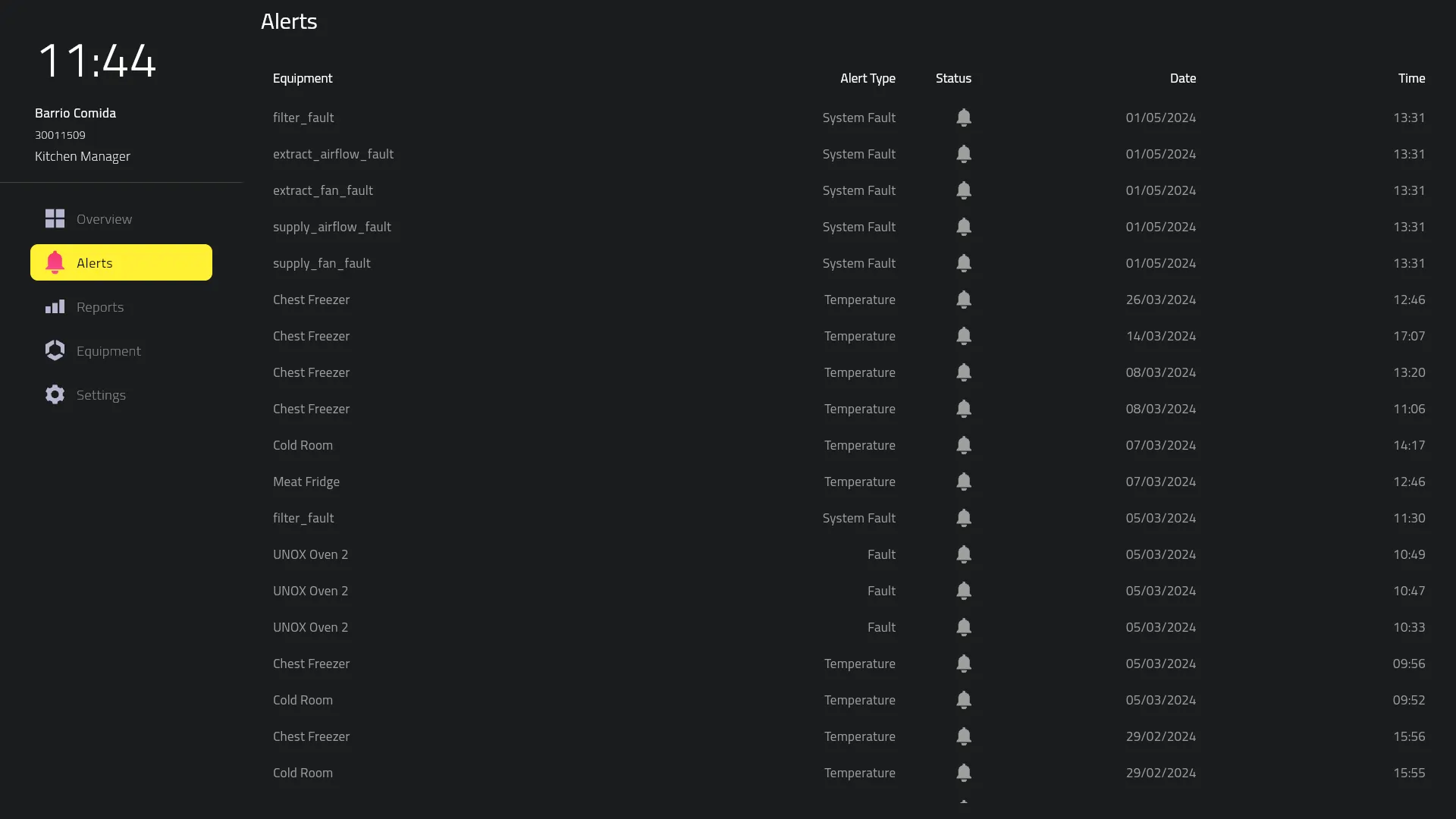
Key Platform Features
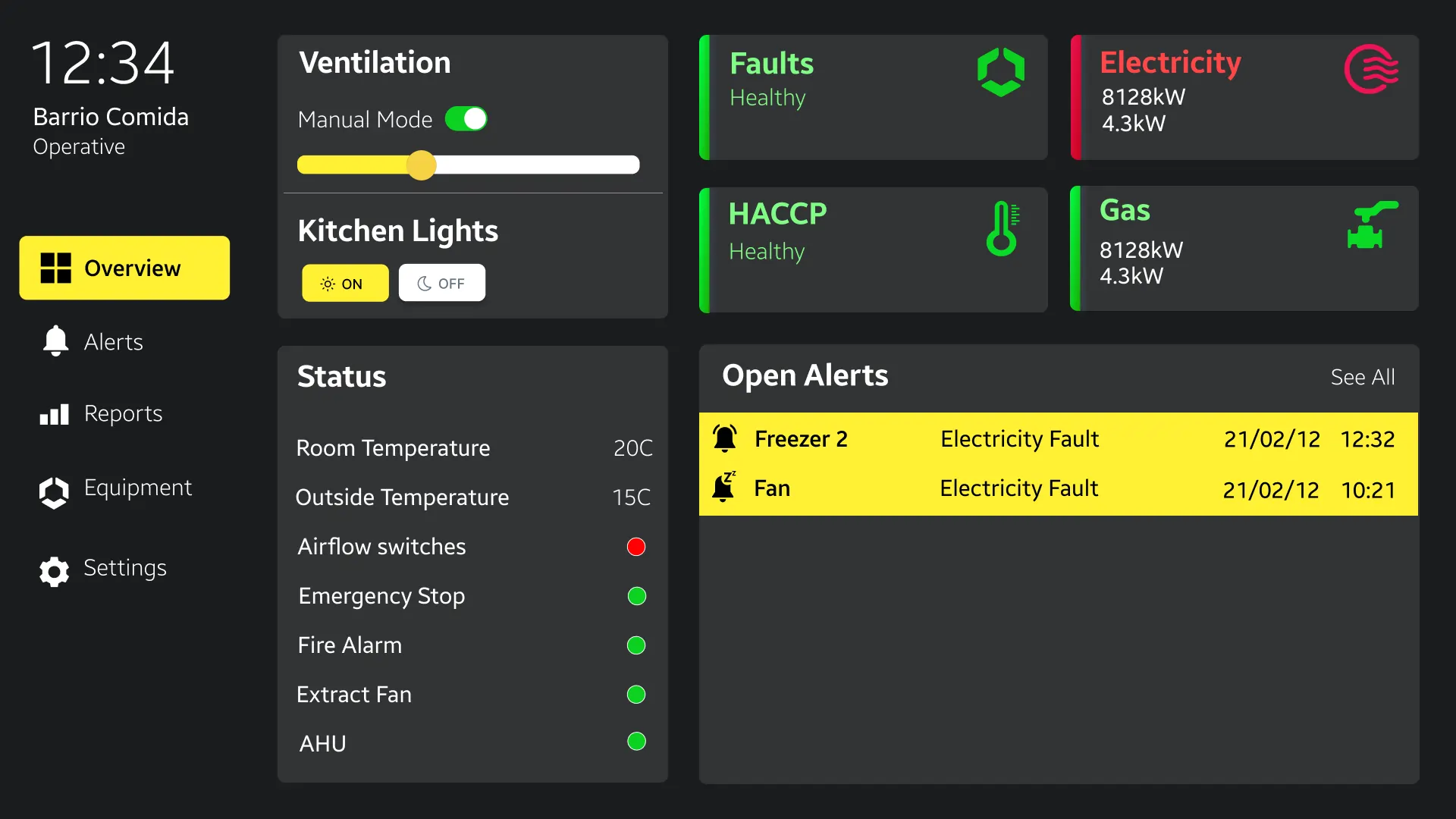
1. Comprehensive IoT Dashboard
The Kioti Kitchen Management System's dashboard provides a comprehensive overview of your kitchen's operational status, allowing you to monitor and control critical aspects of your kitchen environment. The intuitive interface displays real-time data from various components, ensuring that you have the information you need to make informed decisions and maintain optimal kitchen performance.
Key features include live environmental data monitoring room temperature and outside air temperature with instantaneous updates, equipment health status identification, HACCP temperature compliance for food safety, air quality monitoring for Carbon Monoxide (CO) and Carbon Dioxide (CO2) levels, system status monitoring, ventilation and lighting control, and an open alerts summary for quick review of latest alarms.
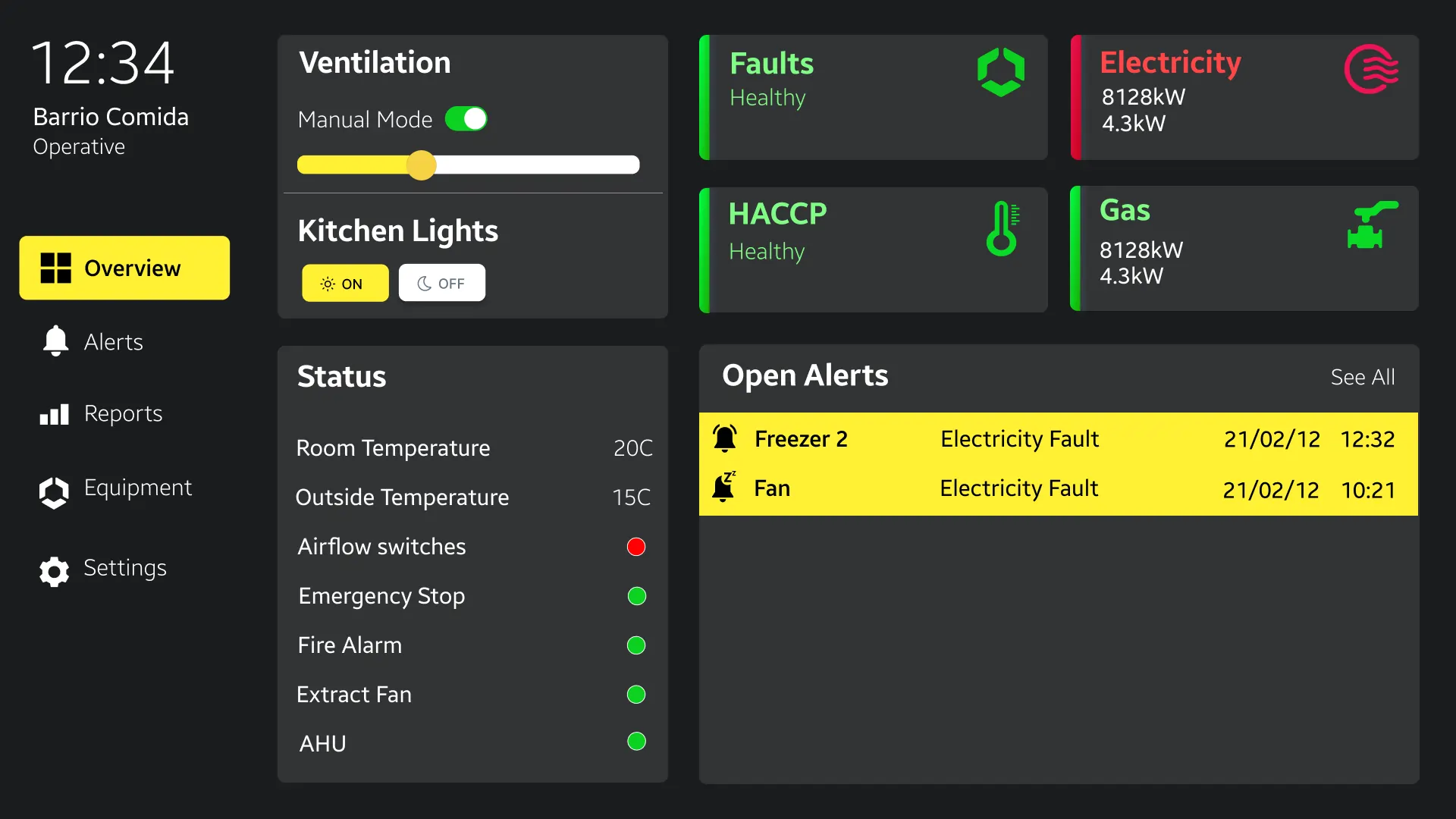
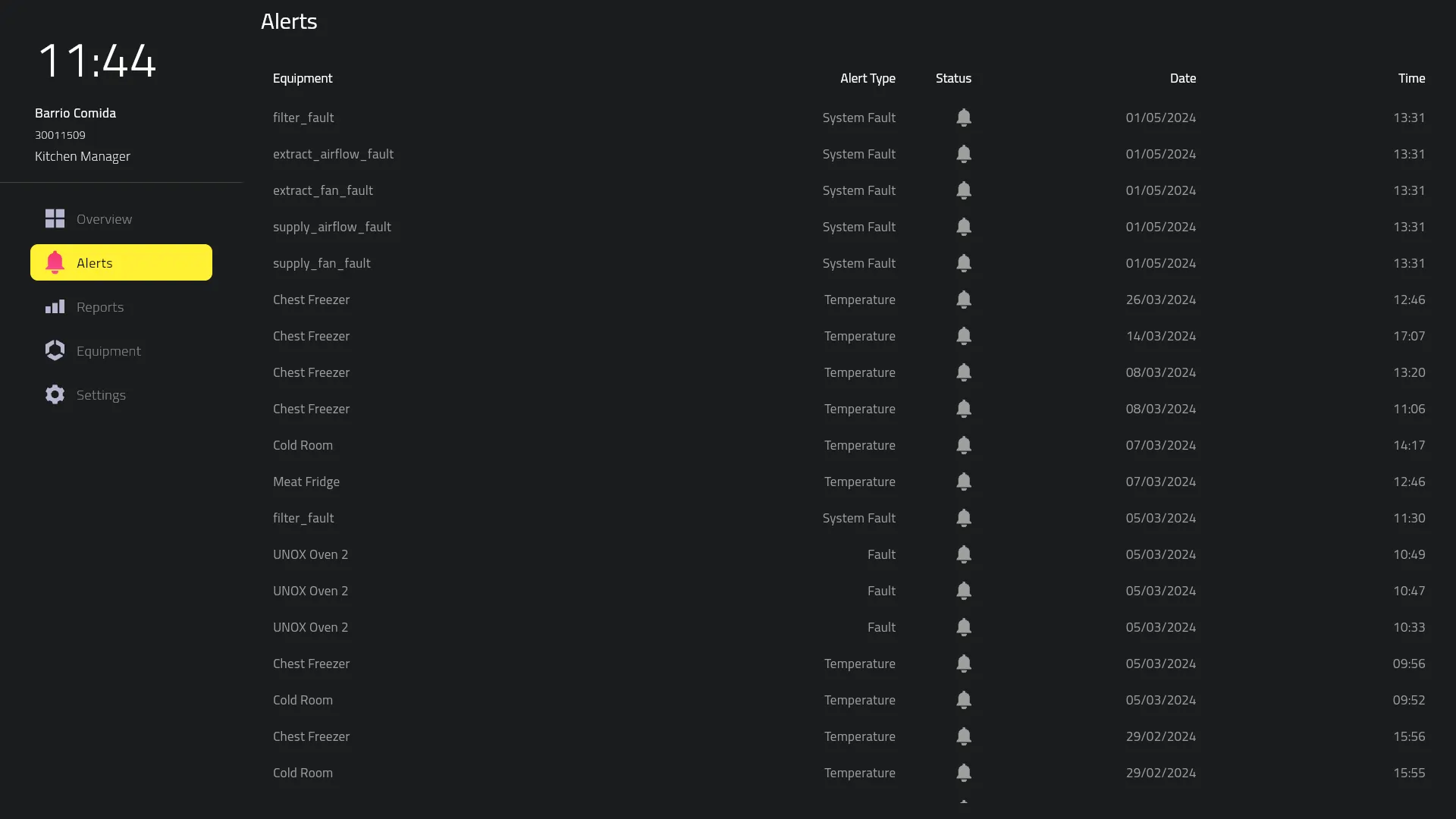
2. Centralised Alerts System
The Alerts screen serves as a centralised log of all alert events, including equipment faults, temperature alerts, and system faults. This comprehensive history allows you to review and analyse any critical events that have occurred in your kitchen, helping you identify patterns, optimise processes, and prevent future issues.
The alerts system provides a chronological alert history with complete, time-stamped records of all alert events, detailed alert information for each incident, and alert grouping functionality that allows you to quickly identify related alerts by selecting an alert to view it alongside other alerts from the same device. This enables rapid diagnosis and resolution of issues.
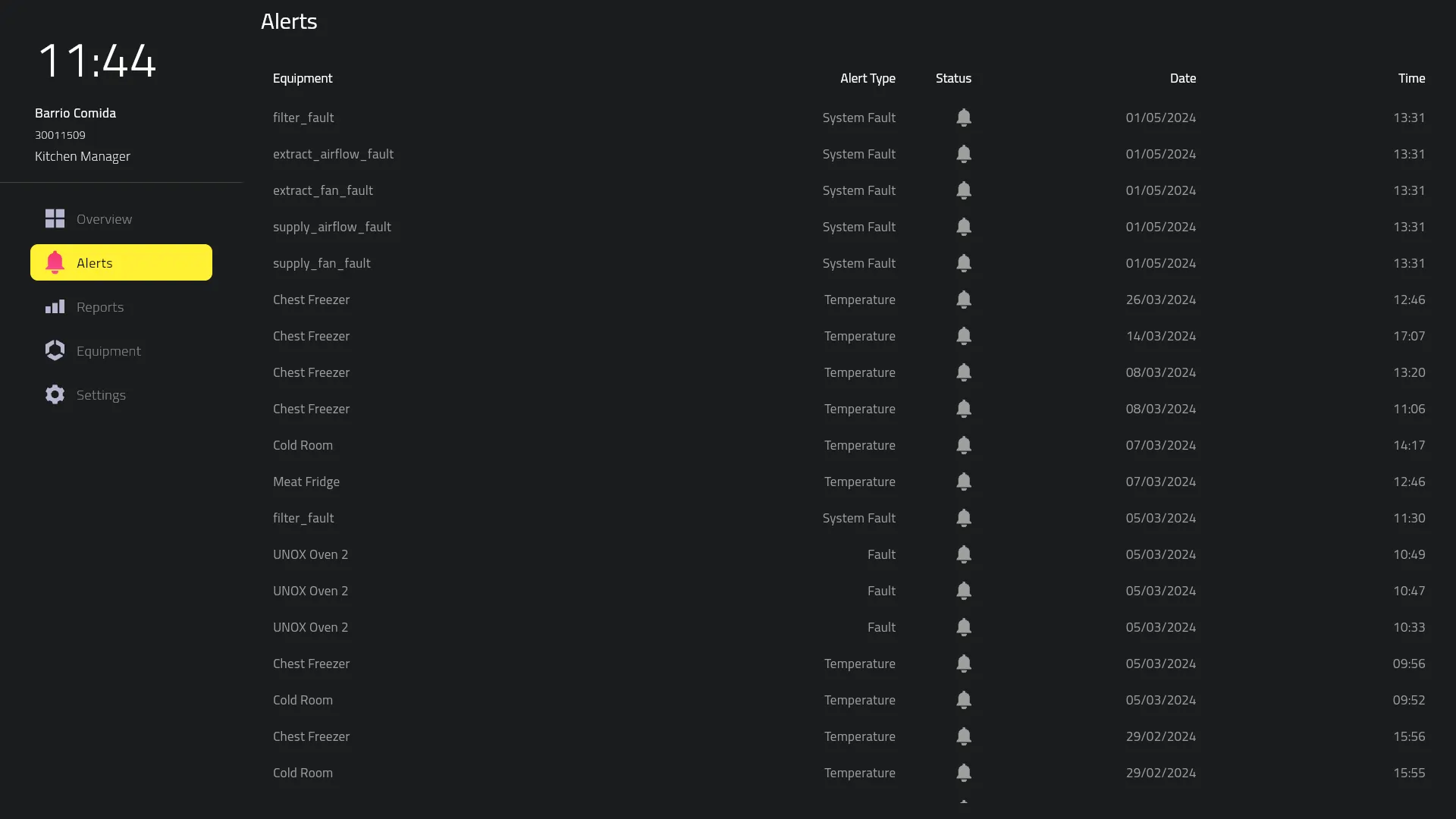
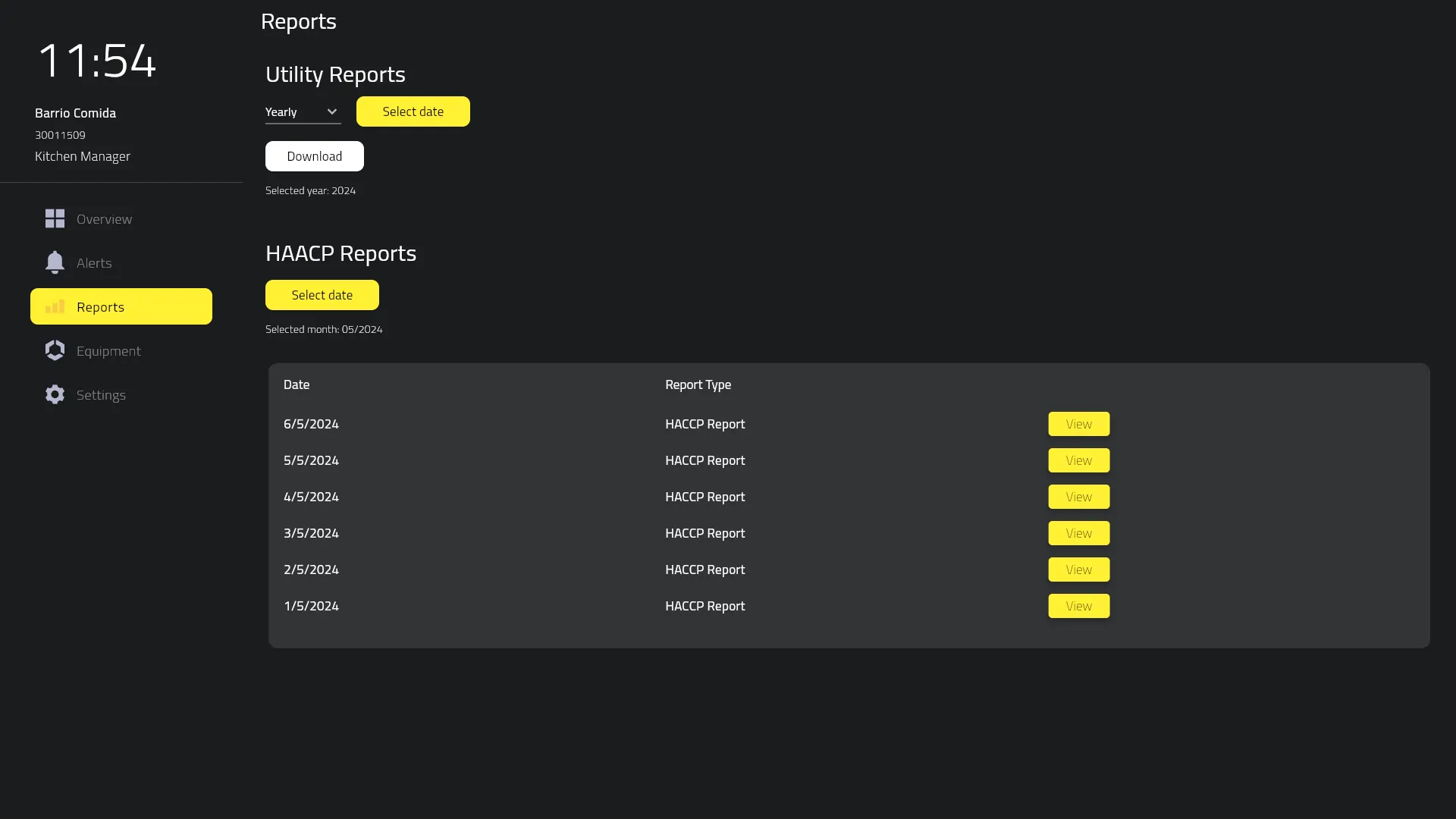
3. Automated Reporting System
The Kioti Kitchen Management System generates comprehensive reports that provide valuable insights into your kitchen's performance, energy consumption, and compliance with food safety regulations. The reporting system ensures you stay compliant with HACCP requirements while optimising operational efficiency.
Key reporting features include daily HACCP temperature reports automatically sent via email, monthly utility reports detailing your kitchen's usage patterns, customisable date range filtering to locate specific reports, and PDF download functionality for easy sharing, printing, or archiving. This automated approach saves time while ensuring regulatory compliance.
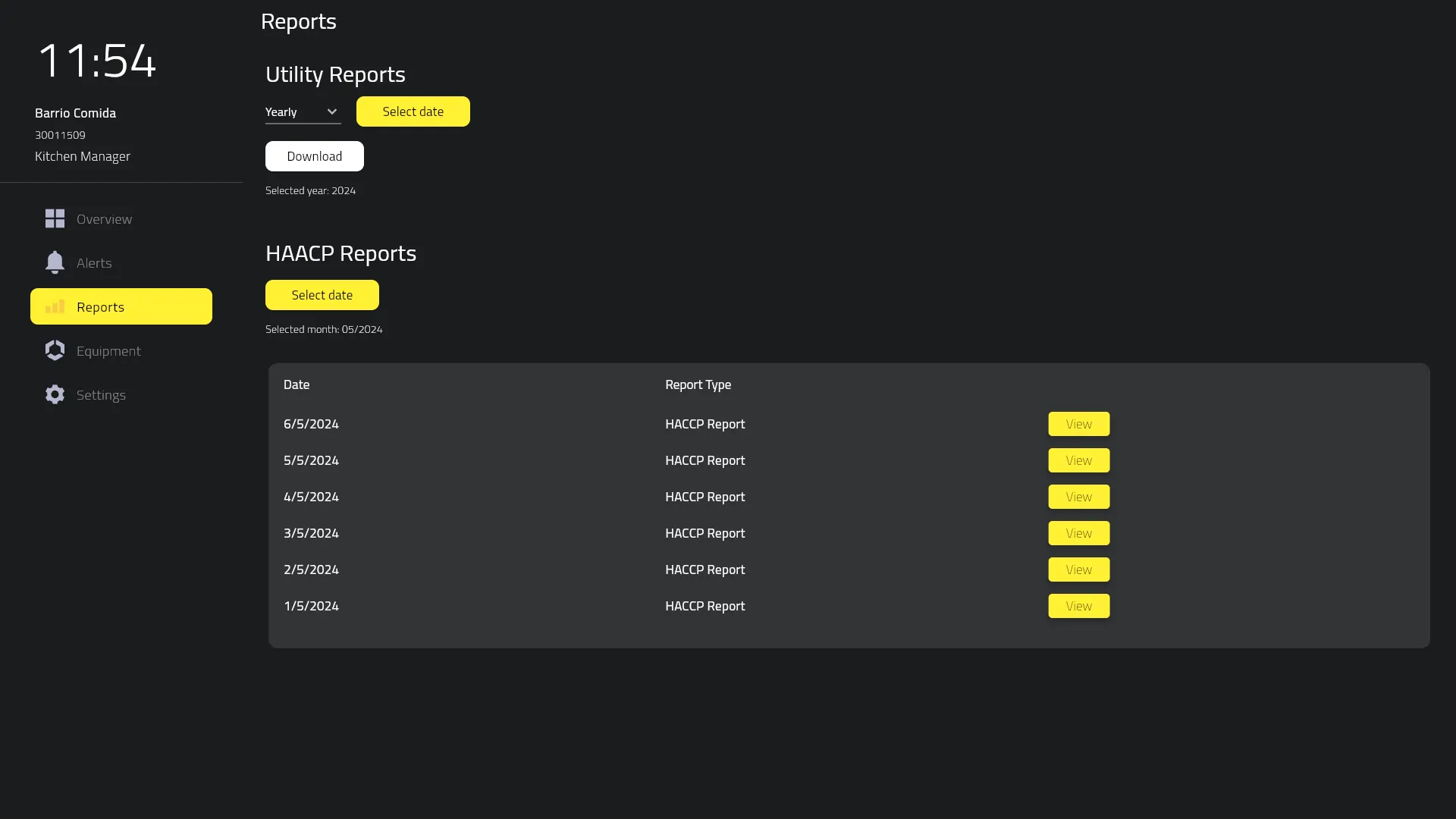
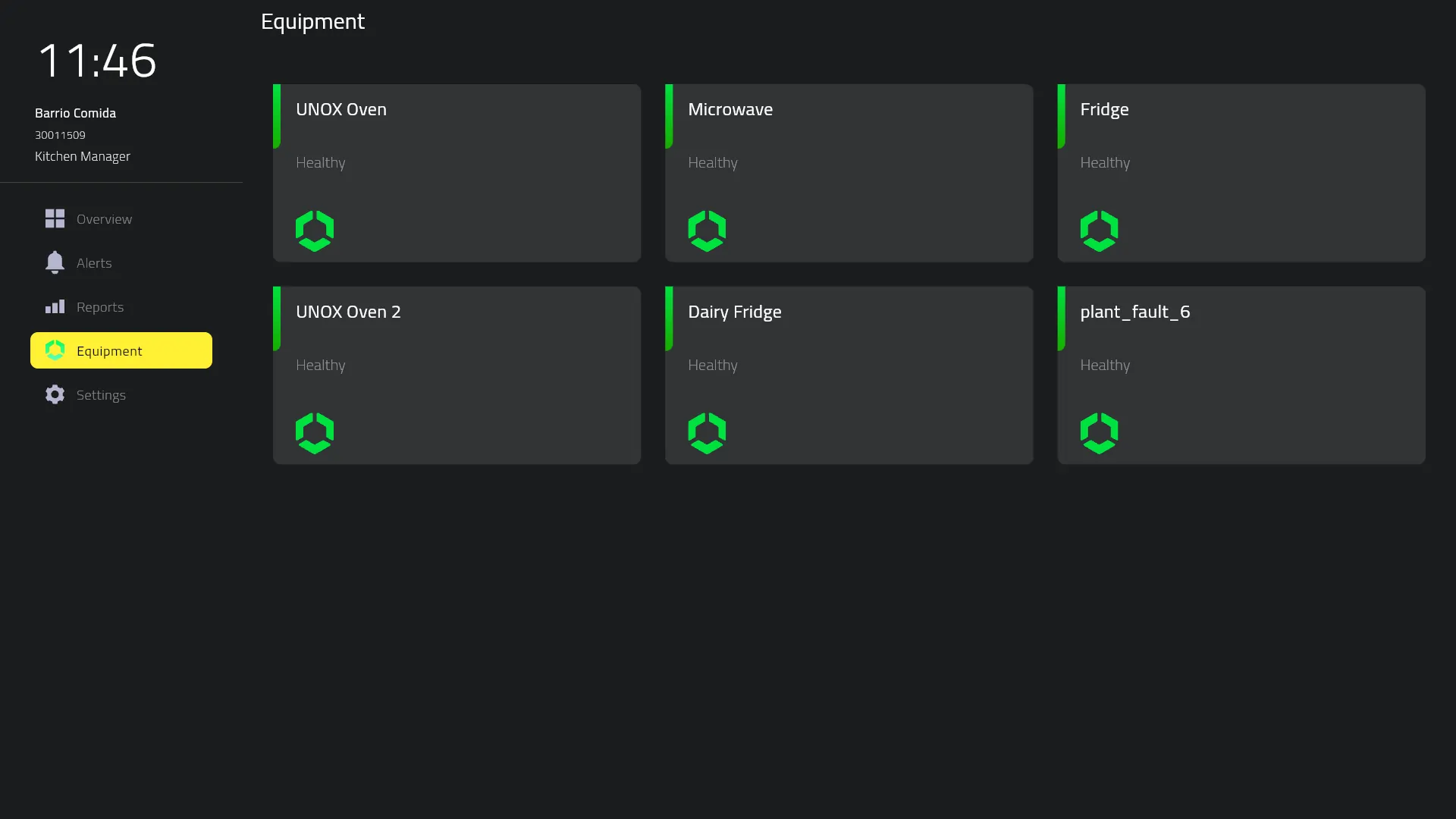
4. Equipment Management Hub
The Equipment screen provides a centralised view of all the equipment connected to the system, allowing you to monitor their status, track fault history, and manage equipment-related information. This comprehensive management system ensures optimal performance and predictive maintenance capabilities.
Equipment management features include real-time equipment status monitoring with visual indicators, installed equipment inventory tracking, comprehensive fault history analysis, customisable equipment naming for user-friendly identification, and complete fault lifecycle tracking from occurrence to resolution. This enables proactive maintenance and reduces unexpected downtime.
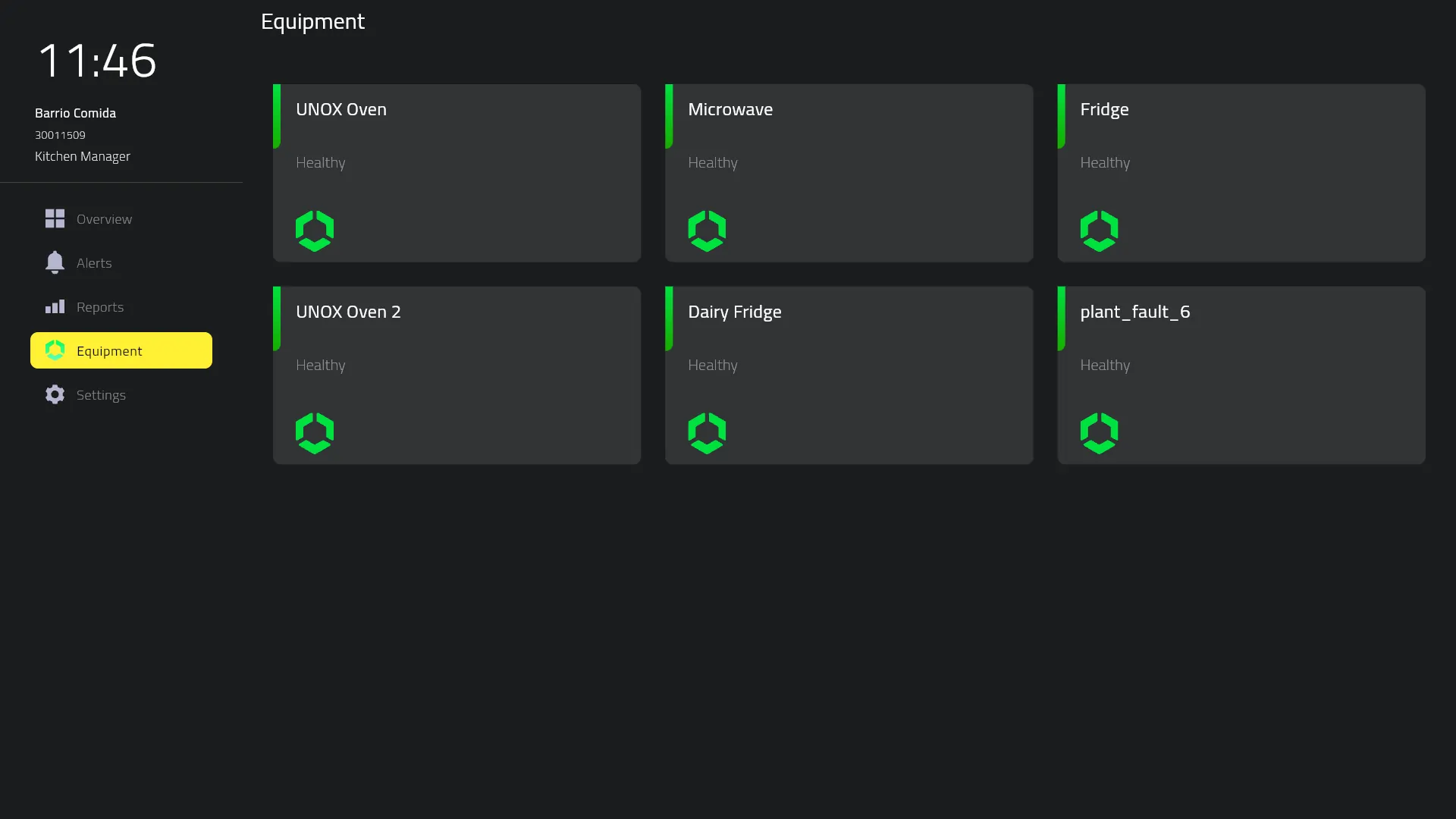
Results and Impact
The Kioti platform delivered a comprehensive IoT solution that transformed how UpNorth Group manages their dark kitchen operations at scale:
Data Processing Power
Successfully processes over 1000 data points per hour across multiple kitchen locations, providing real-time insights into equipment status, environmental conditions, and compliance metrics.
System Reliability
Achieved enterprise-grade reliability with robust error handling and redundancy measures ensuring uninterrupted operation even during hardware or network issues.
User Experience
Delivered a highly responsive frontend that adapts seamlessly to various devices and screen sizes, with an intuitive Tesla-style interface that kitchen staff find easy to navigate.
Compliance Automation
Automated HACCP temperature reporting and compliance monitoring, reducing manual oversight while ensuring food safety regulations are consistently met across all locations.
The Return on Investment
Operational Transformation
- 1000+ data points per hour processed across national kitchen network
- 50+ sensors per kitchen monitoring temperature, air quality, and equipment status
- Real-time alerts and notifications preventing equipment failures and compliance issues
- Automated HACCP reporting reducing manual compliance overhead
Technical Excellence
- Enterprise-grade reliability: Fault-tolerant design with 99.9% uptime
- Scalable architecture: Built to support national expansion
- Intuitive interface: Tesla-style design reduces training requirements
- Mobile optimisation: Seamless experience across tablets and smartphones
Client Testimonial
"Working with OpenKit proved to be a thoroughly enjoyable and collaborative experience - they were quick to adapt to Industry specific challenges and applied their expertise in software development to deliver an enterprise grade full stack IOT solution. I was impressed with how creatively they were able to produce solutions when faced with complex and unexpected scenarios - in this regard, their suggestions and capacity as consultants added great value to the project, improving and refining elements of the initial brief."
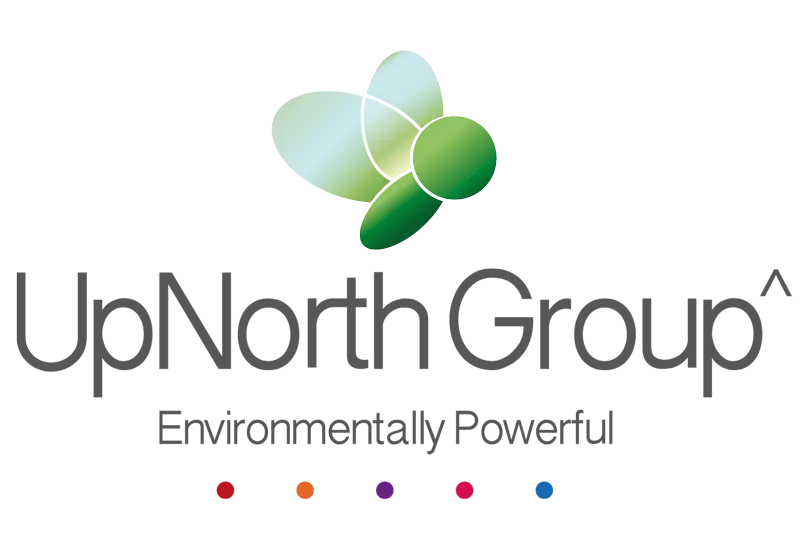
Charles Lewis
Software Development Manager at UNG
Why This Matters for Your Business
Kioti's success demonstrates what's possible when you need to build enterprise-grade IoT solutions that handle real-world complexity. We didn't just create monitoring software – we built a platform that scales nationally while maintaining the reliability that critical operations demand.
If your organisation needs to monitor complex operations, requires enterprise-level reliability, or faces industry-specific IoT challenges that generic solutions can't address, this approach could transform your operational capabilities.
Ready to build enterprise-grade IoT that actually works?
We specialise in complex IoT implementations, SCADA systems, and enterprise solutions that need to work reliably at scale. If you're facing industry-specific challenges or need a system that processes massive amounts of real-time data, let's discuss your requirements.